Welcome to the TECHNOGENIA Inc. Web Site
TECHNOGENIA PRESENTATION OF THE COMPANY AND HISTORY OF LASERCARB
For over 30 years, Technogenia, the leader in the anti-wear protections, has brought to customers the best quality through the state of the art laser cladding technology. Using its proprietary manufactured spherical cast tungsten carbide combined with the latest laser cladding technology, LaserCarb® brings the best solution for effectively eliminating your wear problems.
- 1979: Creation of Technogenia, in France.
- 1983: Beginning research of ‘Cold Crucible’ Tungsten Carbide fusion with electromagnetic levitation.
- 1986: Implementation of the ‘Cold crucible’ system of Tungsten Carbide fusion by induction.
- 1987-1988: Launch of Technosphere® and Technocasting® process.
- 1990: Beginning research on Carbide deposition using high power laser.
- 1992: Introduction of LaserCarb®
- 1993: Installation of a 5 KW CO2 laser, start up of the industrial phase.2000: Research on Diode Laser.
- 2003: Technogenia introduced LASER CLADDING TECHNOLOGY, in Great Britain, with the implementation of a new high power diode laser.
- 2005-2006: Implementation of the diode technology at Technogenia S.A in France.
- 2008: Opening of the United State plant in Conroe, Texas.
- 2009: Introduction of LaserCarb® ID an internal Laser cladding process
- 2011: Oklahoma City Plant Opened.
- 2013: Technogenia Western Canada Opened
LASERCARB
Lasercarb® by Technogenia, the innovators of hardfacing process technology, are strategically applying Technolase® powder with Spherotene®, a spherical cast tungsten carbide, to extend the wear life of new and worn components against abrasion, erosion and corrosion in these industries:
- Mining Tools & Equipment
- Foundries
- Brick & Clay
- Boiler Tube
- Tool & Die
- Construction Equipment
- Agricultural Equipment
- Food Process
- Plastics
- Oil & Gas Downhole Tools
- Tunneling Bits & Equipment
- Pumps and Valves
WHY LASERCARB
Numerous industries use tools that require high resistance to abrasion and erosion. The LaserCarb process is a hard surfacing process that adds an anti-abrasion material to wear parts. The LaserCarb process resolves numerous problems caused by welding. LaserCarb uses powders based on cast Spherical Tungsten Carbide produced by Technogenia.
PRINCIPLE
The process consists of using the energy of a Laser beam to melt the deposition powder (Ni-Cr or other material) on the part.
A weld occurs between the deposit and the base metal.
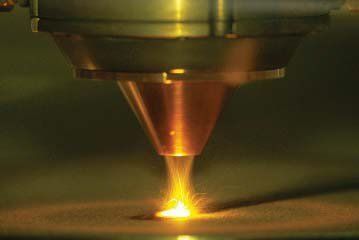
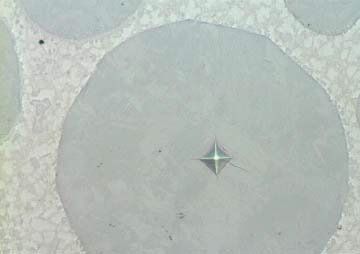
BENEFITS
The hardness and toughness of Spherotene® (cast tungsten carbide spheres produced by Technogenia) united with the unique properties of a high energy laser produces a weld deposit. The cast spheres exhibit hardness of 3000 ± 500 HV, and they pack close together to produce a dense deposit. The spherical shape also increase toughness in the carbide grain and the overall deposit.
- Use of powders based on cast spherical Tungsten Carbide Spherotene®
- High hardness: 3000 HV ± 500
- Spherotene® is not affected by LaserCarb®
- Low heat affected zone (0.060")
- Almost total absence of porosity
- Limited cracking and deformation
- Large range of thickness deposit
- Metallurgical bond
- Precision, Automation, Reproducibility
LASERCARB BENEFITS
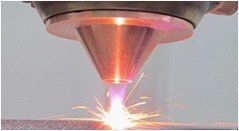
- CNC, 5-Axis automated laser for precise deposit
- Extremely high deposit efficiency
- High hardness factor 3000 HV, low heat affected zone (.060”)
- Virtually no porosity, minimal to no deformation
- High range of thickness deposit
- Numerous combinations of powders, application-specific
- Superior metallurgical bond
- Applied to Carbon steel, Stainless steel, Non-mag stainless steel
- Can be applied to virtually any profile
THE LASERCARB PROCESS
Utilizing a high energy laser with the unique properties of Spherotene® cast tungsten, a superior weld deposit (hard facing) is applied to components to guard against abrasion, corrosion and erosion.The spherical shape of the tungsten carbide when combined with the application specific deposition powder provides an extremely high hardness of 3000 HV + 500.
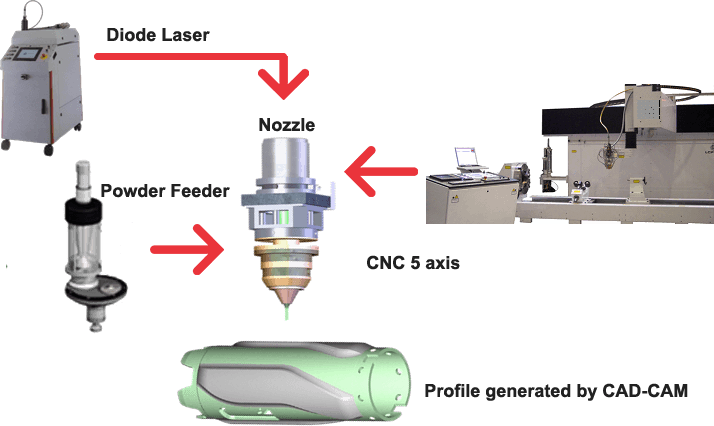
PRIMARY APPLICATIONS
- Oil and Gas
- Wear bands
- Stabilizers
- Drill collars
- Mud Motor components
- Radial bearings (Patent No. 8,795,794, B2)
- MWD, LWD tools
- Tunnel boring
- Pump industry/impellers, wear rings
- Mining
- Paper industry
- Ceramics industry
- Foundries
- Cylinders and rollers in the steel industry
RECOMMENDED TYPES OF BASE MATERIALS
- Carbon steel
- Stainless steel
- Non magnetic stainless steel
- Duplex, Super Duplex
OUR PROFESSION: WEAR RESISTANCE!
LASERCARB® SPECIFICATIONS
- Deposit thickness: 0.015" to 0.150"
- Greater thicknesses - Please contact us.
- Capacities: Length up to 40ft.-Diameter up to 20" Weight 10,000 Lbs.
- Due to their extreme hardness, LaserCarb® deposits cannot be machined expect by grinding with diamond tools.
LASERCARB® I.D SPECIFICATIONS
- Deposit thickness: 0.015" to 0.150"
- Capacities: Length up to 40" long
- Minimum diameter 2"
- Weight 6,000 Lbs.
TYPES OF COATINGS
LaserCarb® and LaserCarb® I.D. use Technolase® powders based on Spherotene®, the Spherical cast Tungsten Carbide by Technogenia.
QUALITY
Through metallurgical analysis and mechanical test, Technogenia provides and develops high quality deposits.
TYPES OF COATINGS AVAILABLE
Technopowder | Thickness | Similar to | Application |
---|---|---|---|
Technolase® 40S | up to 0.050 | 40% - 40 Hrc NiCr Matrix 60% - Spherotene® | Hardfacing, erosion and abrasion protection |
Technolase® 20S | up to 0.150 | 40% - 20 Hrc NiCr,Matrix 60% - Spherotene® | Hardfacing, erosion and abrasion protection |
Technolase® 30S | up to 0.150 | 40% - 30 Hrc NiCr,Matrix 60% - Spherotene® | Hardfacing, erosion and abrasion protection |
Technolase® 50S | up to 0.150 | 40% - 50 Hrc NiCr,Matrix 60% - Spherotene® | Hardfacing, erosion and abrasion protection |
Technolase® 60S | up to 0.150 | 40% - 60 Hrc NiCr,Matrix 60% - Spherotene® | Hardfacing, erosion and abrasion protection |
TP 316-316L | unlimited | SS 316 - SS 316L (Austenitic SS) | Build up and/or Repair |
TP 431 | up to 0.150" | SS 431 (martensitic SS) | Repair, wear application |
TP 245 | up to 0.060" | Stellite 1 | Hardfacing, erosion and abrasion protection |
TP 255 | up to 0.150" | Stellite 6 | Hardfacing, erosion and abrasion protection |
TP 265 | up to 0.150" | Stellite 12 | Hardfacing, erosion and abrasion protection |
TP 275 | up to 0.150" | Ultimet | Impact resistance, high toughness |
TP 625 | unlimited | Inconel 625 | Corrosion resistance |
TP 276 | unlimited | Hastelloy C276 | Corrosion resistance |
TP Fe 7 | up to 0.150" | Tool steel | Impact resistance, abrasion, erosion |
TP diam | up to 0.150" | composition: upon request | High erosion and abrasion resistance |
TP Titanium | up to 0.150" | Ti-6Al-4V | Build up and/or repair |
For different coatings, please do not hesitate to reach us at 936-441-4770
TECHNODUR® TECHNOSPHERE®
APPLIED WELDING
Technogenia Rope, Technodur® and Technosphere®, & Technopowders provide significant hardness in applications requiring 30-60Rc, manually applied using the Technokit welding torch.
TECHNOSPHERE®

Spherical Cast Tungsten Carbide Hardness of 3000Hv
TECHNODUR®

Crushed Tungsten Carbide Grains, Hardness of 2000Hv
TYPICAL APPLICATION
Drill bits, Stabilizers, Wear pads Mixer blades, Conveyor screws Agricultural tools, Mining tools
BENEFITS
- Exceptional abrasion resistance
- Unequalled wear resistance
- Economic and reliable weld
- No deformation of component
- Multiple layers
- Crack free
Product | Thickness of the deposit | Main grain size | Bead diameters | ||
---|---|---|---|---|---|
T E C H N O |
D U R |
TECHNODUR®SGT | 0.080" to 0.160" | 0.005" | 4 and 6 mm |
TECHNODUR®GT | 0.080" to 0.200" | 0.010" | 4 and 6 mm | ||
TECHNODUR®GN | 0.100" to 0.250" | 0.020" | 4-6 and 8 mm | ||
TECHNODUR®GG | 0.100" to 0.300" | 0.035" | 6 and 8 mm | ||
TECHNODUR®TGG | 0.150" to 0.400" | 0.060" | 6 and 8 mm | ||
T E C H N O |
S P H E R E |
TECHNOSPHERE®GF | 0.080" to 0.200" | 0.010" to 0.015" | 4 and 6 mm |
TECHNOSPHERE®GN | 0.100" to 0.250" | 0.015" to 0.030" | 4-6 and 8 mm | ||
TECHNOSPHERE®GG | 0.100" to 0.300" | 0.030" to 0.050" | 6 and 8 mm | ||
TECHNOSPHERE®TGG | 0.150" to 0.400" | 0.050" to 0.090" | 6 and 8 mm |
The need to protect your wear parts differs depending upon the way they are used, their fields of application and level of wear. The Techondure® and Technosphere® ranges offer the complete answer, being specially adapted to your abrasion problems.
PRIMARY APPLICATIONS
- Stabilizers, Drill bits, Wear pads
- mixer blades
- conveyor screws
- Scrappers
- and many other applications.
Please feel free to contact us for further information
OUR PROFESSION: WEAR RESISTANCE!
TECHNOPOWDERS FOR SPAY
Cat. | Item | Crushed Carbide Hardness | Sphérotène® Carbide Hardness | Carbide size | Carbide Concentration | Base Alloy | Alloy Hardness | Melting point | Deposit density | Recom. Deposit Thickness |
---|---|---|---|---|---|---|---|---|---|---|
Powder NiCr | MB40 | no | no | NiCr | 40 HRc | 1087 °C | 8.2 | 0.020" - 0.120" | ||
Powder NiCr | TP 60 RC | no | no | NiC | 60 HRc | 1038 °C | 7.8 | 0.040" - 0.080" | ||
Powder WC | TP 2030 | 2000 ± 200 HV | no | 40-100µ | 40% by weight | NiCr | 60 HRc | 1038 °C | 10.5 | 0.040" - 0.080" |
Powder WC | TP 40/40 | 2000 ± 200 HV | no | 40-100µ | 40% by weight | NiCr | 40 HRc | 1087 °C | 11.2 | 0.040" - 0.080" |
Powder WC Sphérotène® | TP 4000 | 3000 ± 500 HV | 40-100µ | 40% by weight | NiCr | 60 HRc | 1038 °C | 10.5 | 0.040" - 0.080" | |
Powder WC Sphérotène® | TP 4040S | 3000 ± 500 HV | 40-100µ | 40% by weight | NiCr | 40 HRc | 1087 °C | 11.2 | 0.040" - 0.080" |
TECHNOPOWDERS FOR PTA
Cat. | Item | Crushed Carbide Hardness | Sphérotène® Carbide Hardness | Carbide size | Carbide Concentration | Base Alloy | Alloy Hardness | Melting point | Deposit density | Recom. Deposit Thickness |
---|---|---|---|---|---|---|---|---|---|---|
Powder WC | 3000 ± 500 HV | 40-210µ | 60%by weight | NiCr | 40 HRc | 1087 °C | 13 | 0.020" - 0.120" |