LASERCARB ®by TECHNOGENIA
LASERCARB ® Wear Resistance – Uniquely Engineered
Technogenia, innovators of the Lasercarb hardfacing process, is strategically applying its’ proprietary Technolase® powders with Spherotene®, a spherical cast tungsten carbide, to extend component wear life against abrasion, corrosion and erosion in these industries:
- Oil & Gas
- Mining
- Tunneling
- Mixing Equipment
- Geodrilling
- Industrial
- Agriculture
- Construction
LASERCARB ® BENEFITS
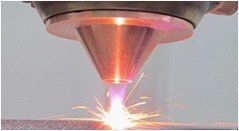
- CNC, 5-Axis automated laser for precise deposit
- Extremely high deposit efficiency
- High hardness factor 3000 HV, low heat affected zone (.060”)
- Virtually no porosity, minimal to no deformation
- High range of thickness deposit
- Numerous combinations of powders, application-specific
- Superior metallurgical bond
- Applied to Carbon steel, Stainless steel, Non-mag stainless steel
- Can be applied to virtually any profile
THE LASERCARB ® PROCESS
Utilizing a CNC controlled, high energy diode laser, a precise, metallurgical weld deposit is applied to the component surface to protect against abrasion, corrosion and erosion. The application-specific Technolase powder matrix in combination with our Spherotene® cast tungsten carbide provides a hardness factor of 3000Hv + 500.
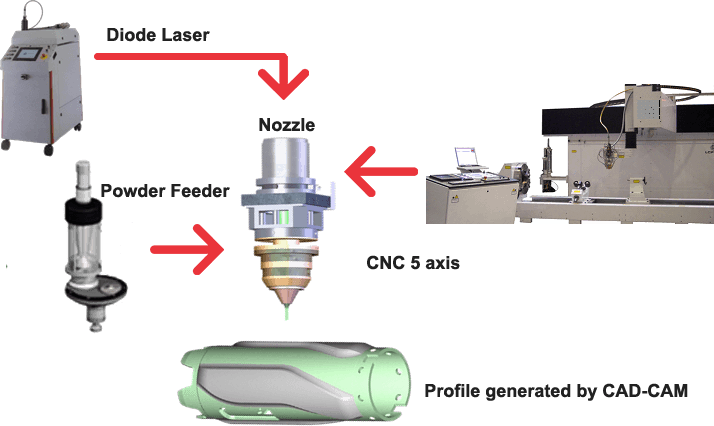
PRIMARY APPLICATIONS
- Oil & Gas:
Stabilizers, Adjusting rings, Bearings (OD and ID) see Patent Details No. 8,795,794 B2, Bearing housings, Drive shafts, Mandrels, Non-mag stabilizers, MWD and LWD tools
- Mining:
Bits, Bearings, Bearing surfaces
- Tunneling:
Bits, Bearings, Shafts
- Mixing Equipment:
Impellers, Mixing blades
- Geodrilling:
Bits, Shafts, Bearing surfaces
- Industrial:
Pumps, Impellers, Shafts, Bearings
- Agriculture:
Soil sample tools, Scrapers, Augers
- Construction:
Bearings, Bearing surfaces, Drive shafts
RECOMMENDED TYPES OF BASE MATERIALS
- Carbon steel
- Stainless steel
- Non magnetic stainless steel
- Duplex, Super Duplex
SPECIFICATIONS
LASERCARB ® SPECIFICATIONS
- Deposit thickness: 0.015" to 0.150"
- Greater thicknesses - Please contact us.
- Capacities: Length up to 40ft.-Diameter up to 20" Weight 10,000 Lbs.
- Due to their extreme hardness, LaserCarb® deposits cannot be machined except by grinding with diamond tools.
LASERCARB ® I.D SPECIFICATIONS
- Deposit thickness: 0.015" to 0.150"
- Capacities: Length up to 40" long
- Minimum diameter 2"
- Weight 6,000 Lbs.
TYPES OF COATINGS
Technolase® powders combine the high hardness of Spherotene® with the unique properties of application-specific matrices to increase anti-wear and erosion protection to the surface of virtually any tool or component profile.
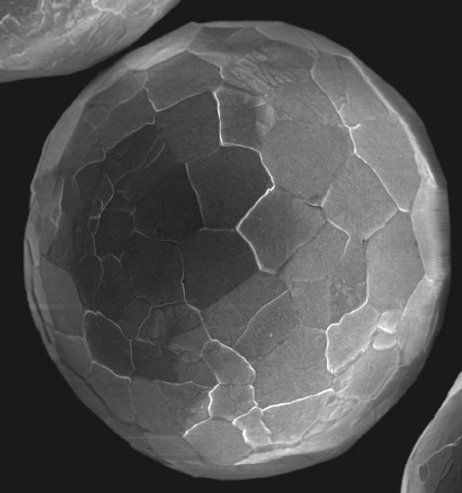
Technopowder | Thickness | Similar to | Application |
---|---|---|---|
Technolase® 40S | up to 0.050 | 40% - 40 Hrc NiCr Matrix 60% - Spherotene® | Hardfacing, erosion and abrasion protection |
Technolase® 20S | up to 0.150 | 40% - 20 Hrc NiCr,Matrix 60% - Spherotene® | Hardfacing, erosion and abrasion protection |
Technolase® 30S | up to 0.150 | 40% - 30 Hrc NiCr,Matrix 60% - Spherotene® | Hardfacing, erosion and abrasion protection |
Technolase® 50S | up to 0.150 | 40% - 50 Hrc NiCr,Matrix 60% - Spherotene® | Hardfacing, erosion and abrasion protection |
Technolase® 60S | up to 0.150 | 40% - 60 Hrc NiCr,Matrix 60% - Spherotene® | Hardfacing, erosion and abrasion protection |
TP 316-316L | unlimited | SS 316 - SS 316L (Austenitic SS) | Build up and/or Repair |
TP 431 | up to 0.150" | SS 431 (martensitic SS) | Repair, wear application |
TP 245 | up to 0.060" | Stellite 1 | Hardfacing, erosion and abrasion protection |
TP 255 | up to 0.150" | Stellite 6 | Hardfacing, erosion and abrasion protection |
TP 265 | up to 0.150" | Stellite 12 | Hardfacing, erosion and abrasion protection |
TP 275 | up to 0.150" | Ultimet | Impact resistance, high toughness |
TP 625 | unlimited | Inconel 625 | Corrosion resistance |
TP 276 | unlimited | Hastelloy C276 | Corrosion resistance |
TP Fe 7 | up to 0.150" | Tool steel | Impact resistance, abrasion, erosion |
TP diam | up to 0.150" | composition: upon request | High erosion and abrasion resistance |
TP Titanium | up to 0.150" | Ti-6Al-4V | Build up and/or repair |